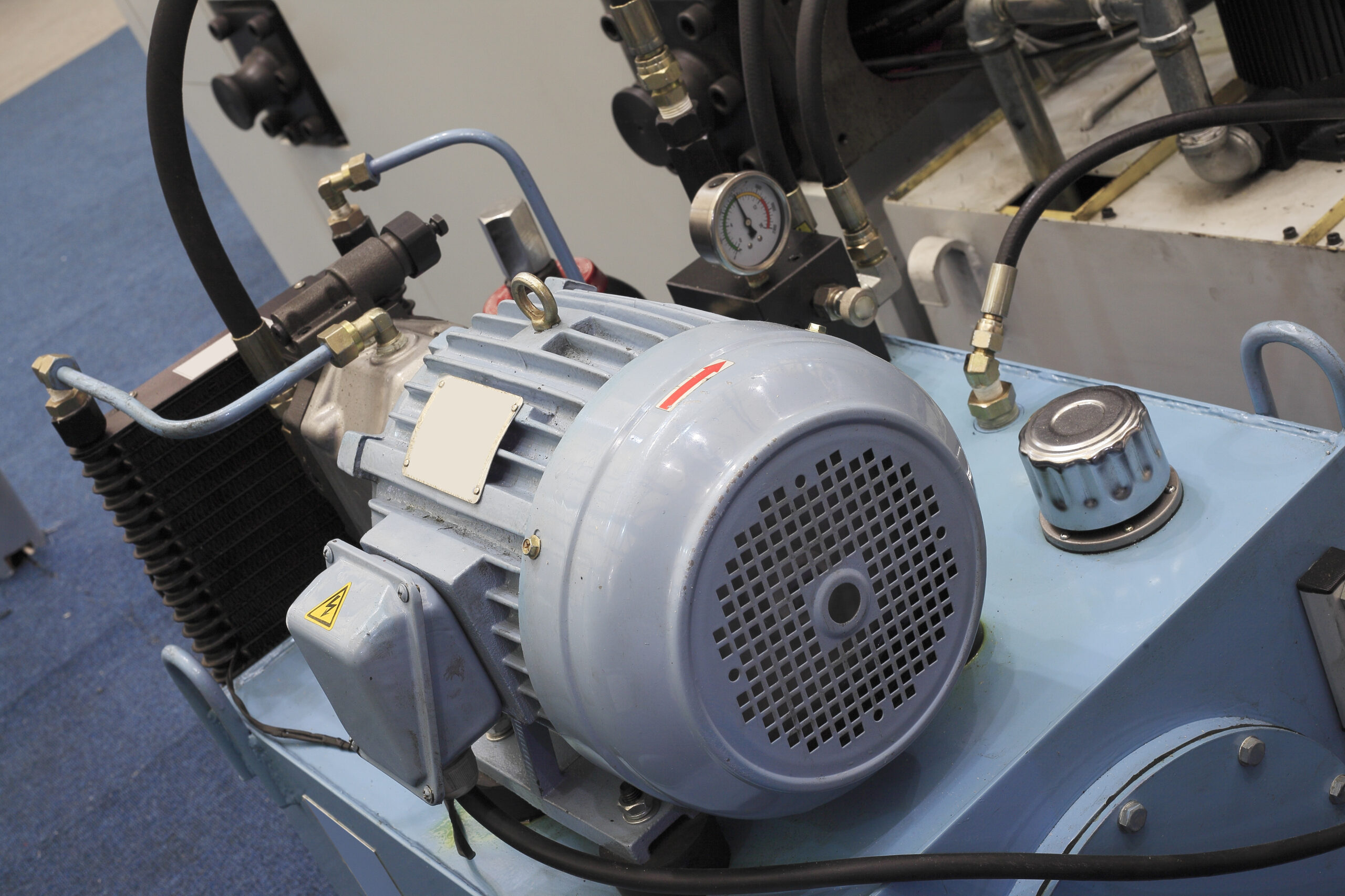
Last week, we looked at how virtual commissioning could offer a cheaper, faster way to fix machine vibration issues. Fundamentally, this post outlined how digital twins (and virtual commissioning) offer you much more than the promise of better machines to come. The underlying technology of digital twins can help you solve a variety of problems you’re facing with machines you’ve already design, produced, or even shipped to customers. This week we’ll look at fixing motor burnout issues, which is another common issue that can plague new machines with uncertain loading profiles.
What causes motor burnout? In simple terms, motors burnout (or fail prematurely) when they are subjected to high duties than they can handle – when the work required of the motor is too high. In our case, this is often from using a motor to move loads that are either too heavy, or to move loads too quickly – any reason that increases the required force to move the load. Overloading of this nature causes excess heat to build up in the motors, which can drastically reduce their lifespan, and, in some cases, cause fusion damage that breaks the motor altogether.
There are many practical ways to avoid motor damage, from ensuring that heat doesn’t build up too fast, or that heat can properly dissipate from the motor. But what happens when you’re faced with fixing motor burnout on your machine? Of course, the solution is going to involved a replaced motor, but the problem may still remain. Do you simply purchase a larger motor, or slow down your machine in an attempt to reduce the burnout issue? Both of those solutions have the potential to prevent future issues, but they don’t give you the precise, root causes of the burnout.
What if, instead, you had the ultimate diagnostics manual for that machine – information that could go beyond steady-state load calculations, and show you exactly how your loading profile impacted your motor?
Using A Digital Twin to Determine Root Causes
This is where a digital twin-based approach stands to really help with fixing motor burnout. With the right kind of digital twin, you’d be able to hone in on the root cause of your issue – an issue that could stem from vibrations, load spikes, or some other unexpected factor. The general process of solving your issues with a digital twin will look similar to the process from last week – so here’s just a brief summary. Note that, when time is really of the essence, many digital twin software vendors will offer their services to both create your digital twin and diagnose your issue.
- Create a digital twin of your machine, either by using software such as MapleSim.
- Validate the model by comparing simulation results from machine performance data, adjusting parameters to ensure fit.
- Analyze the results of digital twin simulations, looking for unwanted load spikes, vibrations, or any result outside of normal behavior.
- Determine a solution based on the results of your digital twin-based analysis (we’ll go into this below).
- Connect your digital twin to the PLC to test the impacts of the proposed solution, such as a target motor size or new motion profile.
Scenario #1 – Undersized Motor

In this scenario, the results of your digital twin simulations are showing that the loading profile is outside of your motor’s operating range. If you need to maintain a certain machine speed (cycle time), then you’ll probably need a larger motor. With the results from your digital twin, you’ll have the exact information you need, and can prevent an unnecessarily large motor replacement (and all the costs that come with it). If you’re using hardware from Rockwell Automation or B&R, tools like MapleSim can export their simulation results so that you can use them within tools like Motion Analyzer or SERVOsoft. Lastly, a bit of virtual commissioning will ensure that this new motor will work with your existing control code, and reduce the time you need to spend on-site troubleshooting potential commissioning problems.
Scenario #2 – Problematic Motion Profile
In this scenario, you’re still seeing the same issue flagged as before: overloading the motor during some of the duty cycle. In this scenario, however, let’s say that the load spikes are found to be at only certain moments during a full cycle – often when moving payloads from a resting position.
Here’s where a digital twin solution shines. Of course, you could either just pay for a bigger motor, or slow the machine down altogether, but these both present costs to you. Instead, what if you could intelligently modify the control code to remove the load spikes, without impacting the cycle time?
If you connect the digital twin to your control code, you can now run simulations so quickly that optimization routines can start to offer big advantages. Using results from these simulations, you’ll be able to slow down the machine at the exact moments where load spikes occurred. In addition, you’ll be able to speed up your machine at other places where loading isn’t an issue. This technology shines for even complicated machines and motions, where in some cases, adjusting the actual motion path itself can offer the same results as having to slow anything down. In essence, you’re just applying a clever optimization that ensures the best performance for a given motor size. In this situation, you’ll have fixed your motor burnout issues without the need for bigger hardware or slower cycle times.
How Can I Trust my Results?
One of the main comments I hear from people is, simply, “How can I trust these simulations to model my actual machine?”. That’s a valid question, and the answers are multi-faceted. While simply showing case studies of successful projects does technically show the promise of digital twins, there’s more we can unpack to gain trust in the process. We’ll cover that next week.