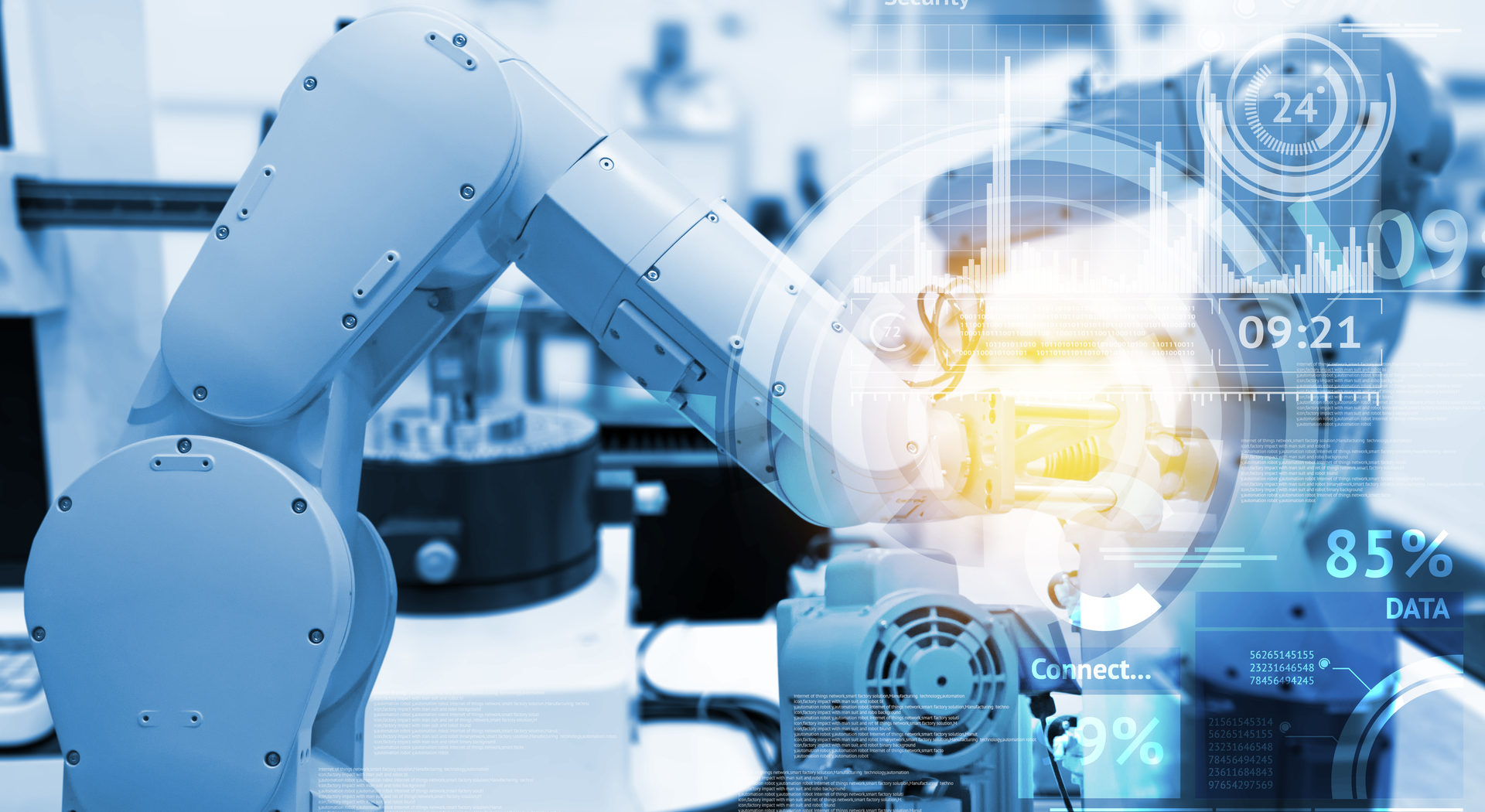
In the simplest terms, virtual commissioning is the practice of using “virtual” simulation technology to “commission”—design, install or test—control software with a virtual machine model before you connect it to the real system.
While commissioning is a crucial part of the process, it typically occurs rather late in development. And while it accounts for only 25% of development time, it’s during this phase that most of the delays occur (Hoffmann et al. 2010). In fact, it’s predicted that up to 70% of delays are a consequence of errors in the control software (Reinhart and Wünsch, 2007). Therefore, the aim of using virtual commissioning is to allow for early validation of machine code. This vastly reduces the risk of deploying a program containing errors. The most time-consuming aspect of commissioning and ramp-up phases comprises software implementation or software redesign. Hence, implementing virtual commissioning also enables higher quality software, and shortens the overall commissioning time.
Since its inception, the intention of commissioning in a virtual environment has been to help solve problems that arise when manufacturing systems are brought together for integration and operation with a PLC. The automation industry has long acknowledged the potential benefits of using virtual models to simulate the performance of physical systems. To be successful, however, the virtual plant model must be an accurate representation of the system in question. While these models had some prominence in the aerospace and automotive industries, their implementation was previously lacking in automation. To achieve implementation, companies needed plant models that integrated with their PLC design methods – something unavailable by early standards.
The Evolution of Virtual Commissioning
Virtual commissioning was first envisioned almost 20 years ago as a promising technique to assist machine development (Auinger et al. 1999). However, the hardware capabilities did not perform PLC testing at an acceptable cost, especially with the real-time simulation requirements when using hardware PLCs. But technology does not sit still. In 2006, Zäh et al. showed that virtual commissioning could save up to 75% of the time required for commissioning.
Many technological barriers have been overcome to realize the benefits of model-based system integration. The current state of technology offers practical techniques that are more accessible than ever to the automation industry. As part of a growing need to speed development and minimize the risk in developing new, innovative products, digital twins and virtual commissioning techniques are quickly becoming essential technologies. But how exactly does virtual commissioning work and what is a digital twin?
How it Works
You’re likely familiar with traditional commissioning but, just in case, let’s explore this from the ground up. The difference between real physical commissioning and virtual commissioning is that a real commissioning process involves testing directly on a real manufacturing system (i.e. a machine), a real controller (i.e. PLC), and other necessary devices, including sensors and actuators. Virtual commissioning, however, uses virtual replicas of the system’s components and has several configuration options.
Virtual commissioning of a machine’s dynamics combines three important pieces: a digital model (sometimes referred to as a digital twin), the controller code that governs the motion and responds to sensor feedback, and a development environment that allows the two to run together.
For this to be practical for the manufacturing and automation industries, virtual models need to be sufficient for their usage outside of niche experts. The development of advanced, model-driven design practices has taken form in a digital twin. Besides the digital twin, the software standards for model connectivity have also seen drastic improvements. Together, these technologies are permitting the widespread practicality of virtual commissioning throughout the automation industry.
With the right tools in place, organizations can adopt virtual commissioning techniques for their machine design projects. They may use these techniques in order to reduce their overall commissioning time, to reduce commissioning costs, or to create a more reliable time to market for reputation purposes. While the applications and specifics can vary, a typical virtual commissioning process has many commonalities.
The Benefits of Virtual Commissioning
One major advantage is that it brings forward the commissioning phase. By using virtual prototypes, manufacturers can test control software in parallel with other engineering phases (Reinhart and Wünsch,. 2007). This vastly reduces the risks of errors later in the development process.
Virtual commissioning also allows testing to be performed in a virtual environment. This commissioning approach allows for improved software quality and increased safety for workers. It also reduces the risk of damaging machinery if tests are carried out in real-time. And that’s just the start – commissioning with a digital twin brings so many more benefits to the table.
Thinking Forward
In the manufacturing and automation industries, adopting new development techniques has become a key requirement for success. As demands on product requirements increase, design risks pose significant problems, threatening the success of those trying to keep pace. The technique of virtual commissioning promises to reduce the significant delays and costs associated with system integration and commissioning. While previously only possible by niche experts, powerful modeling tools and compatible information standards have paved the way for modern, accessible virtual commissioning solutions. This technology is heavily invested in by companies and research groups around the world, creating powerful techniques for model-based design. As these technologies develop, their role in the automation industry will continue to grow into an essential component of product design. Curious about how to get started with Virtual Commissioning? Read more here.
References
- Auinger, F., Vorderwinkler, M. and Buchtela, G. (1999). “Interface driven domain-independent modeling architecture for ‘soft-commissioning’ and ‘reality in the loop'”, Proceedings of the 1999 Winter Simulation Conference, Phoenix, AZ, USA, 1, pp. 798-805.
- Hoffmann, Peter et al. (2010). “Virtual Commissioning Of Manufacturing Systems A Review And New Approaches For Simplification.” In: ECMS. Kuala Lumpur, Malaysia, pp. 175–181.
- Reinhart, Gunther and Georg Wünsch (2007). “Economic application of virtual commissioning to mechatronic production systems”. In: Production Engineering 1.4, pp. 371–379.
- Zäh, M. F., Wünsch, G., Hensel, T. and Lindworsky, A., (2006). Nutzen der virtuellen Inbetriebnahme: Ein experiment, ZWF Zeitschrift fuer Wirtschaftlichen Fabrikbetrieb, 101, 10, pp. 595-599